Janitor Training, Machine Maintenance Extend Life Of Equipment
Should you be Analyzing Your Support Staff Compensation More Often in Elmira, NY, 14901 - ACS Facilities Services
Go To http://www.acsfacilities.com/ for free articles.
Larger machines, such as extractors, aren’t as frequently used as vacuums, but when deployed, the demands on them are heavy-duty. Consequently, the majority of these big machines are built to last — meaning that when they do break down, the repairs can be fairly expensive, especially if a key component like a pump fails, says Bland. Still, he adds, even if the pump costs $500, repair would be worth it on a machine that has performed reliably and could cost thousands to replace.
The type of repair will often tip the scales towards other options. Bushert says that some clients decide to purchase a new machine or have their equipment shipped for reconditioning in the event of a large failure, such as one involving battery packs or drive systems.
“Some clients replace when repair costs reach 50 percent of a new machine,” says Bruce Bushert, president, USA-CLEAN, Inc., a refurbished equipment distributor in Decatur, Illinois. “Others use as high as 70 percent.”
But some repairs fall into the DIY category and don’t require major surgery, such as when an end user can easily access what needs replacing, says Bushert.
“In other words, you don’t have to dive into the inner workings of the unit to replace a part to get your machine going again,” says Bushert. “Also, any basic filters or common wear items are fair game.”
For some BSCs, replacement is simply a business practice. They will replace larger machines every six years or 2,000 hours of use, says Bushert.
Again, an ounce of prevention is worth a pound of cure, and, prevention should become a habit. When it comes to extractors, users should be sure to keep solution and waste tanks empty and clean with the ventilation or tanks open when not in use to prevent mildew growth, says Bushert. Keep solution filters clean and the spray jets free from dust and lint. Winterize units operating in freezing temperatures by using an antifreeze-like windshield washer fluid to flush out the pump and lines.
And pay attention, says Bushert.
“Sometimes it’s possible to anticipate a failure with a loud vacuum motor or a slight leak in a quick connector that will soon turn into a bigger leak,” he says. “The rule of thumb here is to look and listen to anything that is different in the operation of your machine. Changes in sound or loose items will indicate a maintenance need or upcoming failure.”
The Human Equation
During his time as a service technician for JD Distributors, Inc., Cook has pretty much seen and worked on it all when it comes to repairing vacuums, wet and dry extractors, and other cleaning equipment. Cook attributes at least half of the repairs that come in to human error.
Vacuums in particular fall victim to operator carelessness. Cook has pulled out toys from vacuums and other large items, making one wonder what the person was looking at while using the machine. Tiny objects also wreak havoc. Take bobby pins. These can become stuck in the vacuum and then everything picked up afterwards will become lodged behind the pins, causing an obstruction (thus illustrating the value of inspecting the carpeting before vacuuming). He has even seen cases where users have vacuumed up water. Or, people will forget to replace the bags and this “just kills the motor,” says Cook, mentioning that some intake filters won’t prevent this from happening.
The best defense? A good training program, says Cook, made even more necessary where there’s high employee turnover.
Pamela Mills-Senn is a freelancer based in Long Beach, California.
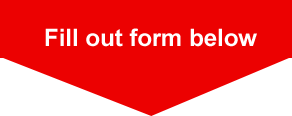