Janitorial Services, Commercial cleaners, Commercial cleaning, Window Cleaning, carpet cleaning, medical cleaning, Odor removal, Office cleaning, Class A Office cleaning, Education Cleaning, School Cleaning, Industrial Cleaning, post construction cleaning, Cleaning services, Green Clean, ACS Facility Services, ACS, ACS Facilities
Go To: http:// www.acsfacilities.com/ for free articles.
Industry 4.0: How Technology is Revolutionizing the Manufacturing Industry
Industry 4.0 might sound like a SimCity-style tycoon game, but it's really the biggest shift to hit global manufacturing since automation. Centered around advanced robotics and automation, new ways of human-machine interaction and vast troves of data and boosted connectivity, Industry 4.0 is poised to modernize manufacturing and boost western industrial competitiveness.
Coupled with the emerging internet of things (IoT), Industry 4.0 offers manufacturers the ability to collect, analyze, and act on immense stockpiles of data like never before, and then set those actions in motion with highly efficient, automated robotics. The result? A higher quality product at a lower operating expense.
What is Industry 4.0?
Industry 4.0, also called manufacturing 4.0, is the marriage of IT and manufacturing operations – the maturation of digital technology in the manufacturing industry. Mark Holleran, formerly the CEO of Xplore Technologies, says it represents a "holistic shift from centralized to decentralized manufacturing," which requires the adaptation of processes, talent, business structure and technology.
"Technology, including advanced robotics and artificial intelligence, sophisticated sensors, cloud computing, IoT, data capture and analytics, and digital fabrication ... are all coalescing into the ushering in of this next industrial revolution," Holleran told Business News Daily.
Here's a look at some of the major components paving the way forward for manufacturing 4.0 and how they work. Together, they create a high-tech ecosystem of smart devices that achieve an optimized, efficient workplace.
Internet of things
As the number of smart devices and amount of data captured, analyzed, and stored grows, connectivity and communication will only become more important. Both within the enterprise and to third-party partners, companies will need their data to be shareable and compatible to enable a higher level of operation.
Declan Keir-Saks, director of Deskera, said IoT is the bridge that allows the granular insights provided by high tech solutions to join together into a coherent, enterprise-level picture for modern manufacturers.
"IoT manufacturing enables virtual tracking of capital assets, processes, resources and products," Keir-Saks said. "This gives enterprises full visibility, which streamlines business processes and optimizes supply and demand."
When implemented correctly, decision-makers will be equipped with more and better information, automated processes, and the ability to intervene on a predictive or preventive basis to avoid downtime or any other issues that might ding production output.
Artificial intelligence and machine learning
The information delivered by sensors and IoT-driven systems is too vast for humans to reasonably analyze. AI and machine learning algorithms can contextualize the data and flag anomalies or make recommendations.
"[AI and machine learning] can help detect early warning signals of assets [becoming] unhealthy," said Derick Jose, co-founder and chief data scientist at Flutura Decision Sciences and Analytics. "For example, top-drive RPM temperature anomalies could be [the] signature of an impending breakdown."
Moreover, AI serves to improve efficiency in the overall operation, Jose said. By quickly returning predictions on the impact of minor changes, decision-makers can understand the effects before they implement something new.
AI is specifically useful when it comes to digesting the massive flows of information captured by sensors and IoT-enabled devices. Those vast troves of data would be nearly impossible for a human operator to contextualize, so allowing computers to do it actually makes that captured data valuable.
Mixed reality
Mixed reality is also a major component of Industry 4.0. Big companies are already issuing mixed reality devices like helmets and glasses to employees in hopes that the increased communication and visualization of contextualized data will boost productivity and intelligent decision-making.
"Mixed reality is a real game-changer in manufacturing," Tim Lynch, CEO of Psychsoftpc, said. "For repair personnel, it allows them to 'see inside' the machine that needs repair or 'see through walls' to the cables and pipes behind to know exactly where to drill or cut."
Couple those capabilities with the predictive maintenance enabled by IoT and AI, and you've got a recipe for high-tech success. If the data suggests a machine is overheating, for example, and the machine-learning algorithms flag it is anomalous enough to warrant dispatching maintenance, workers can employ mixed reality to determine whether a machine is beginning to overheat and precisely which components are affected.
To take it a step further, imagine the maintenance person diagnosing the affected machine recognizes a problem but doesn't have the expertise to fix it. Mixed reality devices can connect someone with the proper expertise to the person on-site, who can then show them step by step, through digital overlays, how to perform the repairs.
For training purposes, mixed reality creates an environment where employees can experience virtual situations relevant to their job without risking actual equipment or manufacturing uptime.
"In training, workers can practice on virtual products to gain experience that will carry over to the real world," Lynch said. "They can be put in simulated situations that they could face in doing their job and learn how to handle them virtually before being exposed to them at work."
3D printing
3D printers have existed since 1983, though were often only in the hands of large companies. Back then, the term was "rapid prototyping," and they certainly continue to do that today. But it's not just prototypes anymore; 3D printers are also employed in low-volume manufacturing, perhaps to test products or bring samples to trade shows.
"When small companies develop new products and need to make 50 parts to test, or just to bring to a trade show, tooling up for traditional manufacturing can be very expensive," Doug Collins, owner of Avid 3D Printing, said. "They might not have the capital to tackle [traditional manufacturing]. 3D printers allow low-volume production without as much investment so they can save that capital for the other important stuff, like marketing."
As the technology continues to improve, it's more common to find 3D printed parts within larger projects. One example is GE Aviation's 3D printed fuel nozzle, which is part of the CFM LEAP airplane engine. By printing certain components, manufacturers can save time and money to create the same final product.
What are the advantages?
With such immense promise and cutting-edge technology, Industry 4.0 requires a major upfront investment. According to a 2017 survey of 1,000 small and mid-size Canadian manufacturers, for example, digital adopters invested an average of $250,000. For larger businesses, the cost would inevitably be higher. But the expected payoff – connected, smart devices and an automated production process – promises a major return on investment.
"These software systems do more than trade data," said Srivats Ramaswami, CTO of 42Q. "They eliminate much of the human intervention that goes with managing them. This next generation of automation – utilizing big data, analytics and artificial intelligence – is one of the most important drivers behind digital manufacturing and Industry 4.0."
Ramaswami added that the advantages manufacturers stand to reap from implementing those technologies include:
- Increased competitiveness. Outsourcing to low-wage regions of the world was previously an imperative for manufacturers wanting to remain competitive. However, investments in technology are now enabling wealthier countries to compete once again. As a result, Ramaswami said, manufacturers can now choose locations based on "technical capabilities and proximity to consumer demand, rather than decisions driven primarily by wages."
- Increased productivity. Automation, analytics and machine-learning algorithms have taken much of the step-by-step work out of the hands of human operators. That means quicker, more efficient production around the clock, with human operators primarily monitoring and maintaining systems.
- Increased revenue and profitability. Industry 4.0 not only creates a more efficient and higher quality production process, but it enables things like predictive and preventive maintenance and upgrades, which results in lower downtime and less capital expenditure over time.
- Manufacturing process optimization. With more connectivity, shared data and better analytics, closer collaboration along the entire supply chain becomes possible, which could lead to increased efficiency, optimization and innovation in the long run across the manufacturing industry.
"Machine-to-machine communications and integrated systems will drive greater collaboration among producers, suppliers and other stakeholders along the value chain," Ramaswami said.
- Seamless record-keeping and traceability. The immense capture and analysis of data also means better record archiving and search capabilities. This has ramifications from government regulatory compliance to customer satisfaction.
"Unlike traditional relationships where feedback on products and services takes time to gather, the automated closed-feedback loop is an inherent component of Industry 4.0," Ramaswami said. "The seamless record-keeping enabled by digital systems will speed traceability, while limiting liabilities, warranty costs and recalls."
Despite these advantages, the shift is still in the early stage. According to research from Capgemini,only 6 percent of manufacturers are considered "digital masters" that have reached an advanced stage in digitizing the production process.
Still, the movement is real; Capgemini estimates that 76 percent of manufacturers already have a smart factory initiative in the works or currently under formulation. What is clear is that Industry 4.0 and advanced digital technologies will soon become the norm for manufacturing worldwide. Those that adopt early on have a better chance to position themselves favorably in the future.
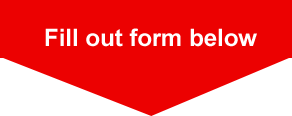