![]() | ![]() |
- Training On Proper Chemical Use
- From: Training On Proper Chemical Use, CleanLink.
For more free articles go to http://www.janiservu.com/

The success or failure of a cleaner, sanitizer or disinfectant is typically not related to the chemical composition of the product, but rather its proper use. When cleaning staff doesn’t understand how to use the products correctly, mistakes happen. It’s up to managers to properly train their staff on these issues to avoid problems.First, it’s critical to review with front-line workers the differences among cleaners, sanitizers and disinfectants. Then, make it clear that the first step in any process must be cleaning and rinsing.“Too many workers believe a sanitizer or disinfectant will also clean, but the surface has to be cleaned and rinsed before you apply the sanitizer or disinfectant,” says Fellows.Janitors may also mistakenly believe a surface is clean if it is free of dirt. Which is why it is important to educate workers on the difference between cleaning for appearance and cleaning for health. While a cleaner alone may be enough to make an area look nice, a sanitizer or disinfectant is often necessary to reach the facility’s desired level of hygiene.“For too long, clean has been a subjective term — determined by a simple visual assessment,” says Hicks. “Two people inspecting the same room or the same object might have a different opinion about whether or not it passes the test. The fact is, surfaces appearing to be clean might not necessarily be clean when scientifically quantified or qualified. Remember, what you can’t see can hurt you. Every department should be striving for health-based cleaning.”It’s also imperative for users to learn that sanitizers or disinfectants require certain dwell times to be effective. Correct usage is to spray the chemical into a cloth, wipe the surface, then wait the amount of time directed on the product label before rinsing the surface. This strategy, according to experts, is most effective at reducing or killing pathogens. It’s also the least harmful method for the worker, who is less likely to inhale blowback from the chemical than with a misting method (spraying directly onto a surface).Safety should always be included in any training program, but is particularly important with chemicals as strong as sanitizers or disinfectants. Facility cleaning managers should review and make sure all staff understands the information outlined on product safety data sheets (SDSs), as well as the location of appropriate personal protective equipment. Training should also include the importance of frequent hand washing when using chemicals, safety protocols for mixing products, and proper storage of the chemicals in a locked and secure location.Finally, cleaning managers may be well advised to seek outside help when determining which mix of cleaners, sanitizers and disinfectants is best suited for their departmental needs. An annual checkup by a consultant may be money well spent to avoid potentially hazardous mistakes and to select the most cost-effective, yet efficient, chemicals for every task.“Most distributors provide free training for products they sell, but if they don’t sell it, they don’t tell it,” says Fellows. “It’s important to stay abreast of the latest technology for cleaning, sanitizing and disinfecting by reading trade journals, attending trade shows or investing in third-party training programs.” BECKY MOLLENKAMP is a freelance writer based in Des Moines, Iowa.
- See more at: http://www.cleanlink.com/hs/article/Training-On-Proper-Chemical-Use--197...
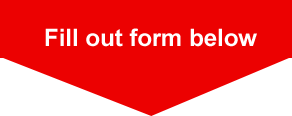