![]() | ![]() |
Hard Floor Cleaning Practices to Consider
Selecting an option based on cleaning results, safety and industry standards.
By Brian Simmons
December 06, 2013
No Comments
KEYWORDS chemicals / finish / floor / hard floor / healthcare / school / scrubber
Print / Reprints /
| Share More
PLEASE GO TO; http://www.janiservu.com/ for similar postings!!
Advantage Cleaning Services Does Janitorial Cleanings In Corning, N.Y. 14836!!
Though there are many types of hard floors and a variety of building environments and sizes, there are a few common elements when it comes to modern hard floor cleaning.
The keys to current maintenance practices are promoting long-term floor life while meeting the immediate requirements of providing a healthy, safe environment.
To meet these principles, common practices include using green chemical solutions, minimizing wet surfaces for slip and fall prevention and minimizing any facility disruptions during cleaning processes or restorative maintenance.
To incorporate these values, facility managers must consider multiple variables when developing a contemporary maintenance plan, including staff experience and training, specific facility needs and equipment.
While all of these are significant to developing cleaning procedures, this article will focus on how selecting the proper equipment can enhance modern cleaning values.
Enhancing Floor Appearance
Stripping and refinishing, among other project-based maintenance activities, are understood to preserve and enhance hard floor appearance, quality and durability.
However, current hard floor cleaning practices incorporate regular, routine maintenance to sustain long-term floor quality.
Although a mop can be useful for cleaning up isolated spills or for maintaining small areas, it can be difficult to meet the increasing health and safety standards using this traditional tool.
Thus, more advanced or automated equipment may be worth considering.
There are specific considerations that should be analyzed when selecting any piece of equipment that is intended to help meet modern cleaning practices.
Green Chemical Options
To reduce chemical waste and excessive water use, some floor cleaning machines include an onboard detergent dispensing system, eliminating the need for manual pre-mixing of detergent and water.
Equipment with onboard chemical mixing systems can provide multiple mixing options ranging from chemical-free, water-only cleaning to detergent solutions that meet the high standards of industries such as healthcare and education.
Typically, floor scrubbers dilute chemicals at a ratio of 128 parts water to 1 part detergent, which is appropriate for heavily soiled floors.
However, facilities that are cleaned on a routine basis often do not require the use of these strong detergent ratios.
Some floor scrubbers have an ultra-low mode that reduces detergent usage significantly to meet regular cleaning needs.
Proper chemical mixing not only promotes environmental and individual health, but it also prevents long-term floor damage and helps maintain floor appearance.
This also minimizes operator exposure to potentially harmful chemicals.
Another equipment innovation, random orbital scrubbing, excels at both daily routine scrubbing and deep scrubbing that is capable of removing floor finish with water only, rather than using stripping chemicals.
These chemicals are some of the most caustic solutions that cleaning professionals use.
The orbital scrubbing provides two simultaneous pad motions, a macro scrubbing motion and an orbital micro scrubbing, to accomplish streak-free clean using less detergent and water and fewer chemicals.
This option reduces potential slip-and-fall injuries, chemical exposure and environmental impact.
Slip And Fall Prevention
Some automated cleaning equipment utilizes vacuum technology that cleans a floor with water or chemical solutions and then immediately dries the floor surface.
This prevents water and solution from seeping into a floor’s base materials, which can lead to long-term damage.
It also improves safety as reducing slip and fall incidents has become a serious concern.
As it has been reported, the U.S. Department of Labor’s Occupational Safety and Health Administration (OSHA), has even revised its Walking and Working Surfaces regulations, requiring that facilities have an effective cleaning process and incorporate more stringent oversight.
To help ensure that the proper precautions are taken, the National Floor Safety Institute (NFSI) — one of several groups that help identify key criteria that should be considered when selecting cleaning chemicals, equipment and procedures — offers independent product testing for equipment and product manufacturers.
One of NFSI’s tests evaluates products’ slip resistance, and incorporating the slip resistance test results with the product makes purchasing decisions easier for end users.
With the aid of such information, facility managers can select the proper equipment and ensure that the most stringent safety measures and guidelines are met.
Minimizing Building Disruptions
Equipment noise level is also important.
Regardless of the facility, using low-noise equipment enhances operator safety without disturbing building occupants.
Finding equipment that operates with low noise is preferable in many settings, especially in schools, hospitals, religious facilities and other noise-sensitive and high-traffic areas.
By utilizing such equipment, facility managers can thoroughly clean floors during business hours.
This ability increases safety, since puddles, soil, spills and other potential hazards can be cleaned without disturbing building occupants.
Going Beyond Appearance
Given the cleaning industry’s technological advances, changing safety regulations and increased facility management standards, today’s maintenance practices go beyond improving a facility’s appearance.
By selecting the proper equipment, facility managers can ensure that modern hard floor cleaning values — promoting long-term floor life and meeting the immediate requirements of providing a healthy, safe environment — are being met.
Green chemical solutions, working to prevent accidents and minimizing facility disruptions are practical ways to exercise those values.
Brian Simmons is a product manager for Nilfisk-Advance Inc., a position he has held since 2003. During this time, Simmons has focused his efforts on all automatic scrubbers in the commercial cleaning markets. For more information, visit www.Nilfisk-Advance.com.
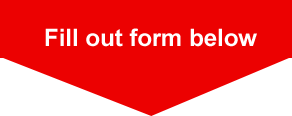