![]() | ![]() |
Oops… I Guess That Didn’t Work!
Become a ‘proactive’ restorer instead of a ‘reactive’ victim.
By Brandon Burton
June 07, 2013
KEYWORDS building / documenting / drying / humidity / restoration / restorers / water
Print / Reprints /
Share on facebook Share on twitter Share on linkedin | Share More
PLEASE GO TO; http://www.janiservu.com/ for similar articles and posts!!
Advantage Cleaning Services Does Carpet Cleaning In Elmira, N.Y. 14903!!
The typical restoration project is a blend of science and art — and for good reason.
Of the great number of variables in each project, many are difficult to identify early in the restoration effort. Often, the restoration project begins with several assumptions in place.
If inaccurate, these assumptions can lead to critical shortcomings that drive up costs, dramatically increase the amount of time needed to complete restoration and even increase risks to health and safety.
The best way to reduce the risks associated with assumption is to ensure a complete and thorough understanding of the variables early in the project.
In this article, we will explore several of the most common assumptions made by restoration contractors, and how to ensure you do not become a victim to each.
Water source
A recent call from a restorer to my office really drove home the importance on this topic.
The property owner said the water source was a broken fresh water line that had been repaired immediately following discovery. The restorer assumed, therefore, it was a clean loss. Water damage, struvctural drying mistakes
After a day of drying, the floor rewet. As it turned out, the true source of water was a blockage in the septic system causing significant grey and black water backup.
A lot of questions could be raised about how a source like this could be overlooked, but at the end of the day, the technician had accepted the property owner’s statement about the source.
A day later, after air movers had been blowing air throughout the building, the restorer was left with dry sewage particulate distributed throughout the structure.
It is imperative that restoration contractors understand the exact nature of water intrusion. Further, it is critical that the source (or sources) be documented and stopped before restoration procedures begin.
Because the water source has so much impact on the necessary cleaning and demolition needed, this is a step that cannot be overlooked.
Water migration
One of the most costly assumptions made by many restorers is an understanding of what is, and more importantly, what is not affected.
The standard process is to begin at the water source and track water migration throughout the structure, documenting what is wet.
There are two mistakes often made in the process:
1. Assuming how the structure is built
2. Documenting only what is wet.
When investigating water migration, it is critical for the technician to avoid assuming which building materials were used to construct an assembly (such as a wall or floor).
Often times, these assemblies contain several hidden surprises, such as multiple finish layers or unusual construction methods. If non-standard methods and materials are not identified and accommodated in the drying setup, they can present substantial drying challenges.
In addition, each area the technician suspects may have experienced water migration should be inspected. And, every area that is inspected should be documented.
Even if water is not discovered, it is critical the result is recorded. Think for a moment: Why did the technician look beneath the cabinets? Because there was reason to believe it may have been wet. If damage occurred previously, and the cabinets are pulled in the future, that damage can be blamed on the contractor, especially if had not been noted that the area was not wet.
High humidity
It is common to see high humidity at the onset or early stages in a restoration project.
However, with appropriate extraction and dehumidification, high humidity should be short-lived. If high humidity persists beyond several hours, something has gone wrong.
Often, however, many restorers respond to high humidity by simply adding dehumidifiers. That indeed sounds simple enough but, believe it or not, it is usually not what is needed.
Abnormally high humidity can be caused by a variety of issues. These include the homeowner turning off dehumidification, intermittent or interrupted power, insufficient extraction, recurring water intrusion, wet areas that were not identified, high outside humidity infiltrating into the structure or a poorly performing dehumidifier. Have you checked that filter lately?
In all of these cases, adding a dehumidifier is not going to help. Choosing the easiest solution may not be the best solution.
If the homeowner is turning off equipment (check your hour meters!), then all you’ve done is add another power button for them to push when you leave.
In all cases, it is critical to ensure you understand the problem correctly. This is best done by learning a lesson from our children: Asking “Why?” again, and again, and again.
The humidity is high: “Why?” Dehumidifiers are not keeping up with evaporation: “Why?” You get the point.
Nature of construction
In today’s world of building construction, remodeling and maintenance, there are a very broad range of materials and practices used by property owners and contractors.
As a result, knowing how a building is put together is probably one of the more challenging aspects of the work we as restorers have to tackle.
You just never know what you will find when you look into an assembly. That interior wall could easily have been an exterior wall at some point.
I’ve even encountered structures where, after some discovery, it was apparent that what was now a home was once a meat packing facility, complete with foam insulation beneath the concrete slab.
No drying process can be deployed without a full understanding of what is to be dried. In addition, the technician has no idea if the project is progressing without knowing what materials need to be inspected and monitored.
Of the challenges this presents, the greatest is the correct metering strategy. Most instruments are severely limited on what they measure, especially non-invasive (pinless) type meters. Usually, this type of instrument will only check a half an inch of material. A half an inch will not cut it for most assemblies.
Pin type meters are a critical part to the process. See my March 2013 article in Cleanfax magazine entitled “The Value of Invasive Moisture Meters.”
Progress
I’ve often made the statement that progress is the single most important item a restorer will document. In reality, documenting what is and is not wet is a close second in importance, as it helps you know where to focus.
Documenting the completion of the project is also important, so you know when to pull off the job. However, what you are actually hired for is to move from wet to dry as quickly and cost effectively as possible. Progress is the evidence of exactly that.
Progress is also what prevents mold and bacterial growth. Progress is what gets you out of the property owner’s life sooner. Progress is everything.
Most restorers, though, do a poor job of documenting progress. In order to do it effectively, you have to have a consistent and standardized process for how your technicians inspect materials.
How do you know if a wall is making progress if your technicians use different meters, or check different areas? It only works if the same meter is used on the same spot.
The next time you inspect a property, check the wall with your meter of choice. Now, move the meter up the wall six inches. Get a different reading? What would happen if you check the first spot on day one, then accidently six inches higher on day two?
To make matters worse, many restoration firms use inspection forms for daily monitoring. An inspection form starts out blank, and all of the first day’s data goes on the form. The second day, another ‘blank’ form is used to capture the data. How do you know if it is improving unless you review the form from the first day?
Consider using a monitoring form that has several days of data, usually in a table, on one piece of paper. Add an average box in the table for each day, and you can see progress (or lack thereof) instantly.
Make it even better with a graph.
Not easy, but worth it
These are just a few of the common areas where restorers can dramatically improve profitability and reduce cost through improved monitoring and inspection.
It isn’t an easy task to tackle, but well worth the benefit. Often, the most challenging part of the information presented here is maintaining a consistent level of training with the technicians who are making daily decisions in the field. Second is getting your field staff to agree that the process of metering must be consistent.
We’ll continue this thought in a future article, addressing additional areas of challenges in the restoration industry. We’ll tackle the issues of common reasons for inappropriate equipment sizing and the pitfalls of misunderstanding customer priorities.
Brandon Burton is the technical education manager for the Restoration Sciences Academy (RSA), a part of Legend Brands. He teaches IICRC-approved classes in the categories of Applied Structural Drying (ASD) and Water Damage Restoration (WRT). Burton has served the restoration community for more than 15 years as an IICRC-approved instructor, ANSI/IICRC S500 chair, RIA restoration council member, and many other industry roles. You can contact him at BrandonB@RSA-HQ.com.
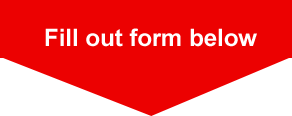