Advancing the Speed of Turning Operations
January 1, 2019
rollFEED turning in use: The interruption-free process is faster than a complex turning operation using several tools by up to 90%.
The specially shaped indexable insert rolls across the workpiece surface during the 3-axis motion.
The process is freely programmable. The resulting complex contours include end faces and cylindrical surfaces, bevels and convex or concave surfaces.
For this process, the EMAG machine is expanded with the rollFEED unit that can be mounted as a driven tool on a turret.
The technological and business competition in the automotive industry is the main driver of change in production technology. Even traditional processes such as turning are constantly improving. For this reason, the geometries of many components are becoming more complex, and the requirements for surface quality are continuing to rise. At the same time, there is pressure to continuously decrease manufacturing costs. Which processes are needed to achieve these goals? The rollFEED turning process (patent pending) by the German toolmakers at Vandurit is providing an answer to this question. The process can be used exclusively with all EMAG vertical turning centers with chuck diameters of up to 500 mm (20"). It expands the turning processes by a third axis, and can be retrofitted. "rollFEED turning offers shortened cycle times, lower tool costs and better surface quality - even at deeper cutting depths. Even complex part geometries can be created in a single motion with just one tool. Customers benefit from a significant leap in performance for the turning of difficult to machine components," said a company spokesperson.
Higher complexity in metalworking often causes longer process times and rising costs. For example, when ball joints, transmission sleeves, gears, bearing rings or shafts with demanding surface requirements undergo many process steps before the desired geometry is achieved, it costs time and money. As a result, production planners are always looking for ways to combine several process steps into a single operation.
"This was the idea behind the development of rollFEED turning," explained Maurice van den Hoonaard, CEO of the Leverkusen-based company Vandurit. "One of our customers wanted to optimize their machining process for a complex part that undergoes turning on three adjacent sides. The previous process with several turning tools was complicated and time-consuming. We revised the entire process and developed a new approach, adding a third axis to the traditional turning process. This enables the insert to move during the machining operation. Now a specially shaped rollFEED insert consisting of radial segments moves along the various sides of the part, one after the other."
The decisive factor is the expansion of the turning center with the rollFEED unit, which can be used as a driven tool on the turret or the tool slide. It can also be retrofitted. The unit functions as a third axis that allows the tool to pivot during the turning operation. The resulting center offset is compensated by the existing X and Z axes of the machine. The specially shaped rollFEED inserts are another critical factor. They roll across the workpiece surface during the 3-axis motion. This causes the point of contact to move to some extent along the tool's cutting edge. "Due to the uniformly or variably sized machining radius segments, it is possible to work with significantly higher feedrates. In addition, the surface quality is better, all the way into the corners. From there, the machining operation continues on to the adjacent side of the component," van den Hoonaard explained.
Marketed Exclusively on EMAG Machines
The technology can be used exclusively with any EMAG turning center, which enables a new cooperation between EMAG and Vandurit. The engineers at EMAG are marketing the process on a global scale. How did this collaboration come about? "We are convinced that this approach opens new potential in turning for many customers, especially if they strive for high surface quality or want to shorten the overall cycle time of their turning operations," explained Philipp Ruckwied, head of technology for defined cutting edges at EMAG. "In addition, our pick-up machines are often designed for the machining of complex components in the course of a holistic process. Several machining steps are running in sequence with a single clamping operation. The philosophies of EMAG and Vandurit are a perfect match."
As a result, the interruption-free rollFEED process is up to 90% faster than multi-step turning operations using several tools. In addition, a complete machining process from three component sides is now possible with only one type of insert. As a result, the number of different tools used in production is lower, which makes many tool changes redundant - a true cost killer. "The technique also achieves extremely high surface quality, comparable to the results of scroll-free turning or grinding," Ruckwied added. "We have already confirmed this successfully in some initial pilot projects. They use the process on VSC and VTC machines by EMAG for hard-machining axle pins, the cages of ball bearings, ball bearing rings, gears and sliding sleeves - precisely those complex parts that we had been focusing on previously. The process time became considerably shorter, and the surface quality is excellent." The development process is still continuing at Vandurit and EMAG. The experts are working on a second stage of expansion. The process will also be available for use in soft-machining processes with EMAG pick-up turning centers in the future.
Both partners see great market potential for this new approach, because rollFEED turning can be used with all relevant materials and is freely programmable with the CAD/CAM system. The resulting contours include, for example, end faces and cylindrical surfaces, bevels and convex or concave surfaces, with internal or external machining. "Complex parts are finished very quickly, with high precision and without tool changes," EMAG's Philipp Ruckwied concluded. "This also benefits customers with existing EMAG turning centers. The rollFEED unit can be retrofitted without problems. These are easy-to-fulfill preconditions that will succeed in the market."
For more information contact:
Kirk Stewart
Sales Director
EMAG L.L.C.
38800 Grand River Ave.
Farmington Hills, MI 48335
248-996-4703
SOUTHWEST
TX, LA
Eric Klenner
Regional Sales Manager
EMAG L.L.C.
248-595-1530
TX, OK, AR
Glenn Wise
Regional Sales Manager
EMAG L.L.C.
248-756-1641
NM
Shane Cross
Regional Sales Manager
EMAG L.L.C.
248-207-5365
SOUTHEAST
MS
Eric Klenner
Regional Sales Manager
EMAG L.L.C.
248-595-1530
AL, GA, FL, NC, SC, E. TN, VA
Dave Fitzgerald
Regional Sales Manager
EMAG L.L.C.
248-595-1117
W. TN
Mark Comeaux
Regional Sales Manager
EMAG L.L.C.
248-938-2097
NORTHEAST
W. PA, WV
Mark Comeaux
Regional Sales Manager
EMAG L.L.C.
248-938-2097
NY, PA, DE, MD, NJ, CT, RI, MA, VT, NH, ME
Kevin Gadde
EMAG L.L.C.
248-938-2430
Portions of NY and PA
Jeff Moore
Regional Sales Manager
EMAG L.L.C.
519-835-8425
MIDWEST
OH, KY, S. IN
Mark Comeaux
Regional Sales Manager
EMAG L.L.C.
248-938-2097
N. IN, W. MI
Peter Vandersluis
Regional Sales Manager
EMAG L.L.C.
616-307-7401
E. MI
Jeremy Elder
EMAG L.L.C.
248-962-8963
ND, SD, NE, KS, MN, IA, MO
Bill Konetski
Regional Sales Manager
EMAG L.L.C.
612-804-0857
IL, WI
Joe Thompson
Regional Sales Manager
EMAG L.L.C.
248-880-0233
WEST
WA, OR, CA, NV, ID, MT, WY, UT, CO, AZ
Shane Cross, CMTSE
EMAG L.L.C.
248-207-5365
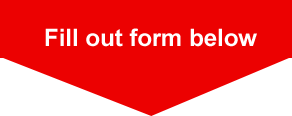