![]() | ![]() |
Static in carpet
By Aziz Ullah, Ph.D., MBA
October 13, 2010
Print / Reprints /
Share on facebook Share on twitter Share on linkedin | Share More
PLEASE GO TO:http://www.janiservu.com/ for similar articles!!!
Advantage Cleaning Services Offers Green Cleaning In Horseheads, N.Y. 14845!!!
Anyone who has walked across a carpet and then touched a doorknob has felt the effects of static electricity.
Uncontrolled static charges are responsible for numerous problems, causing millions, and even billions, of dollars in damage every year.
In the textile industry, static is responsible for the clinging, tangling and breaking of synthetic fibers.
Static can also serve as a natural magnet, attracting dirt and dust to carpet coatings, chemicals, and soil filtration lines.
At its worst, electrostatic discharge (ESD) may cause fatal shocks, as well as fires and explosions where flammable solvents are used.
Most vulnerable to ESD are the electronic and computer industries, where the electrostatic discharge can punch virtually undetectable holes through the metal oxide walls of computer chips.
According to major electronic manufacturers, static electricity accounts for 28 to 60 percent of all field component failures.
While electrostatic charge can''t be totally eliminated, it can be controlled.
The beginnings of static
All matter — whether solid, liquid or gas — is made up of atoms containing positively charged protons in the nucleus and an equal number of negatively charged electrons orbiting the nucleus (Figure 1).
Both charges are equal and, therefore, the overall charge of a balanced atom is zero. The protons in the nucleus are held tightly together, but the outer electrons are held loosely and can move from one atom to the other.
Unbalancing this configuration of electrically non-conductive materials generates static electricity.
Very simply, static electricity usually occurs when two materials are rubbed together (Figure 2).
Upon separation, electrons are transferred from one material to the other.
The material losing the electrons becomes positively charged while the material receiving the electrons becomes negatively charged.
The amount of the charge on the surface depends on the material''s conductivity and its ability to pass along an electric charge.
A good electric conductor, such as metal, loses its charge immediately, while poor electric conductors, such as plastic, paper and fabric, retain charges over long periods — even weeks.
Although rubbing is not necessary for charge generation, it usually increases the amount of charge produced.
Materials getting charged
Series of materials may be listed in orders so that each becomes positively charged by rubbing with those following it.
One such series proposed for textile fibers is as follows: 1. wool 2. nylon 3. silk 4. viscose 5. cotton 6. ramie 7. acetate 8. polyester. 9. acrylic 10. polyethylene
For instance: When wool is rubbed with polyethylene, the wool becomes positively charged while the polyethylene assumes a negative charge because of a greater affinity for the electrons lost from wool.
Such groupings are useful in predicting the signs of generated charges but not the magnitude of the charges.
Problems due to static charges
In manufacturing, static generation can cause difficulties in opening, extruding or carding fibers; in positioning layers of textile materials; and in keeping fabrics lint and soil-free during processing.
Soil and lint pick-up due to static electricity, the clinging of garments to each other and to the body, and the generation of electrical shocks when walking on carpets or sliding over upholstery are also annoying problems for the consumer.
Static electricity generated on fabrics can interfere with the operation of computers and other sensitive instruments, and set off discharges of sufficient magnitude to ignite flammable vapors.
Generally, a charge on a conductive surface will not cause a static problem. The charge dissipates itself by moving to any ground the surface may be touching.
Thus by grounding conductive materials, hazardous static charge buildup can easily be constrained.
However, charges on non-conductive surfaces, such as walking with rubber-soled shoes on a wool carpet in very low humidity can build up the charge so that it becomes repulsive.
The problem — and some remedies
Wool and manmade fibers such as nylon, acrylic and polyester, develop static electricity from friction and use.
As a result, the fibers attract dirt particles — and even spark and cause minor, but discomforting, shock to the user.
All materials, including fibers, vary in their ability to acquire a static charge and transfer this charge from one material to another.
Static electricity becomes more of a problem in the winter months when humidity is low.
The moisture content of fibers and relative humidity of their environment significantly influence their ability to dissipate such charges.
In most instances, it is not advantageous to rely totally on moisture-related fiber properties to dissipate or reduce static charge in textile fibers and fabrics.
For human comfort, the static charge buildup should be kept under 3,500 volts — and for microelectronic systems, at 500 volts or less.
Most fiber producers employ a conductive carbon core to conduct and dissipate static.
DuPont’s warranty states its Antron nylon will not generate static greater than 3,500 volts.
BASF certifies its carpets would not generate more than 3,000 volts.
Aftermarket treatments you can use
The most effective aftermarket treatment is the surface treatment.
Most antistatic agents applied to textiles function by increasing their rate of charge dissipation, although some agents also function by reducing the generation of static charge on the fiber.
A variety of compounds and polymers have been used to impart static resistance to textiles.
This is accomplished by either making the fibers more hydrophilic and thus more prone to dissipate static charge and/or by treating them with a good conductor or polyelectrolyte to achieve such an effect.
Most antistatic finishes or fibers were developed for synthetic fibers with low to moderate moisture content such as polyamides, acrylics and polyesters.
General classes of antistatic agents include various chemicals like amines, amides or quaternary ammonium salts.
Most nondurable antistatic finishes for textiles involve application of surfactants such as quaternary ammonium salts (quats).
The "quats" are not compatible with the stain resistant type carpets and should never be applied to them. In those cases the anionic type antistatic agents must be employed.
For maximum efficiency, the antistatic agents should be present on the surface of the fiber and, in fact, a gradual loss of antistatic protection can be attributed to the tracking off or migration of the antistatic agent into the interior of the fiber.
New technology makes static more dangerous
Clearly, the risk of damage or destruction due to static charge increases with the technological sophistication and miniaturization of products and processes not to mention the nuisance effect it has on people.
Increasing the rate of charge dissipation can control static problems.
The use of conductive fibers by the fiber producers helps in solving problems with static electricity.
If the carpet causes static problems, surface treatment by use of antistatic agents can eliminate these problems.
Since most antistatic agents are cationic in nature, they should be avoided on stain resistant carpet and only anionic type used instead.
Also, avoid using products that claim additional anti-resoil properties, as the materials used are electrically non-conductive, since all they do is negate the charge dissipation properties of the antistatic agents.
Aziz Ullah, Ph.D., MBA is president of Fabpro Manufacturing, is a leading formulator of scientifically engineered carpet and upholstery cleaning products. He is a member of the American Chemical Society, senior member of the American Association of Textile Chemists and Colorists, member of The Textile Institute (UK). He can be reached via his website at www.fabpro.com.
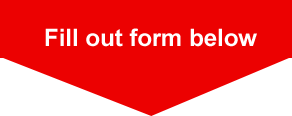